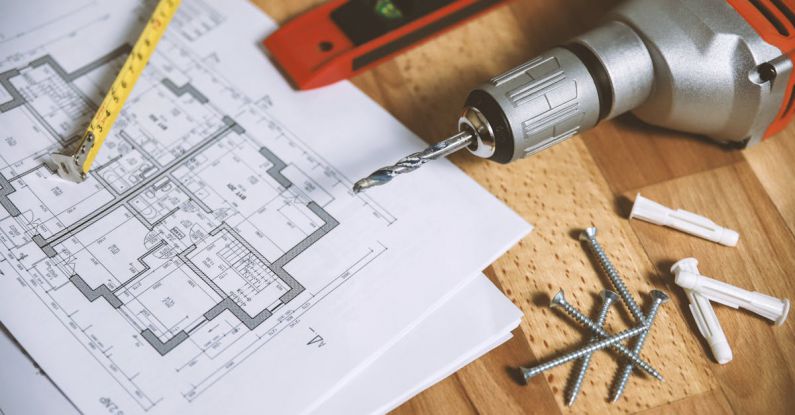
The Impact of 3D Printing on Car Manufacturing
In recent years, the automotive industry has seen a significant shift in manufacturing processes due to the rise of 3D printing technology. This innovative method of production has revolutionized the way cars are designed, developed, and built. The impacts of 3D printing on car manufacturing are profound, leading to improved efficiency, cost-effectiveness, and customization capabilities.
Enhanced Design Flexibility
One of the key impacts of 3D printing on car manufacturing is the enhanced design flexibility it offers. Traditional manufacturing methods often have limitations when it comes to creating complex shapes and intricate designs. With 3D printing, car manufacturers can now easily produce parts and components that were once deemed too difficult or costly to manufacture using traditional methods. This newfound design flexibility allows for more creative and innovative car designs, ultimately leading to vehicles that are lighter, more aerodynamic, and more fuel-efficient.
Rapid Prototyping and Iteration
3D printing has revolutionized the prototyping process in car manufacturing. In the past, creating prototypes for new car models was a time-consuming and expensive endeavor. With 3D printing, car manufacturers can now quickly and cost-effectively produce prototypes of new car designs, allowing for rapid iteration and refinement. This accelerated prototyping process enables car manufacturers to bring new models to market faster than ever before, giving them a competitive edge in the fast-paced automotive industry.
On-Demand Production
Traditional car manufacturing processes often involve large-scale production runs that can result in excess inventory and storage costs. 3D printing has changed this dynamic by enabling on-demand production of car parts and components. Car manufacturers can now produce parts as needed, reducing lead times and eliminating the need for large warehouses to store excess inventory. This on-demand production model not only saves costs but also reduces waste, making car manufacturing more sustainable and environmentally friendly.
Customization and Personalization
3D printing has opened up new possibilities for customization and personalization in car manufacturing. Car buyers are increasingly looking for vehicles that reflect their individual tastes and preferences, and 3D printing allows car manufacturers to meet this demand. From personalized dashboard designs to custom exterior features, 3D printing enables car manufacturers to offer a level of customization that was previously unattainable. This personalized touch not only enhances the overall driving experience but also creates a stronger emotional connection between car owners and their vehicles.
Supply Chain Optimization
Another significant impact of 3D printing on car manufacturing is the optimization of the supply chain. Traditional manufacturing processes often involve complex supply chains with multiple suppliers and long lead times. 3D printing simplifies this process by enabling car manufacturers to produce parts in-house, reducing dependence on external suppliers and streamlining the production process. This optimization of the supply chain results in faster turnaround times, lower production costs, and increased flexibility in responding to market demands.
Future Outlook
The impacts of 3D printing on car manufacturing are undeniable, with the technology continuing to revolutionize the industry in unprecedented ways. As 3D printing technology advances and becomes more widespread, we can expect to see even greater innovations in car design, production, and customization. Car manufacturers that embrace 3D printing stand to gain a competitive advantage in an increasingly competitive market, paving the way for a future where cars are not just manufactured but truly created with precision and ingenuity.